Sheet Metal Bending Machine – Things to Keep in Mind When Shopping
There are many benefits to owning a Sheet Metal Bending Machine. It can help you achieve the bending desired. Here are some things to keep in mind when shopping for one:
Sheet Metal Bending Machine for Roll Bending
A roll bending machine is a sheet metal processing device that pinches the metal between two rolls. The machine is capable of bending a wide range of sheet metal materials, and it accepts a high degree of automation. A typical roll bending machine can bend ovals, rounded boxes, and tube segments. Roll bending machines have the advantage of being simple to operate, as workers can safely operate them.
The process of forming full-tube shapes involves a urethane roller. This material prevents the seam from being uneven. The radius of the curved metal part should be uniform, so it eliminates the need for pre-forming and cutting off ends. Crowning can be done with shim stock, which is wrapped around the bending roll’s middle. However, you should make sure to adjust the shim stock’s diameter to compensate for the deflection. Crowning can also cause a gap at the ends of thin metal parts.
Sheet Metal Bending Machine for Free Bending
When buying a sheet metal bending machine, you should consider what parts you plan to produce. Aim to purchase the machine that has the least amount of tonnage and shortest workbench. You should also consider the type of material you intend to process, the maximum thickness and length of the parts, and how long each part should be. For example, low carbon steel requires a machine with a free bending force of 50 tons, while bottomed die forming requires a 150-ton machine.
While bending the metal sheet, it is important to note that punching causes plastic deformation. When the metal sheet is shaped, the material will experience two distinct plastic and elastic deformations. When a part is shaped, the metal sheet will be in contact with a mold three times and generate three indentation lines – the V-groove shoulder and the plate. These shoulder marks will result in different shapes.
Sheet Metal Bending Machine for Three-point Bending
A sheet metal bending machine can perform three-point buckling, a common form of a crimp. The three-point buckling operation exposes multi-layered strips to a range of compressive and tensile stresses. The stress concentration varies from a maximum at the neutral axis to zero at the outermost surface. The results of the buckling tests are illustrated in Figure 13.4.
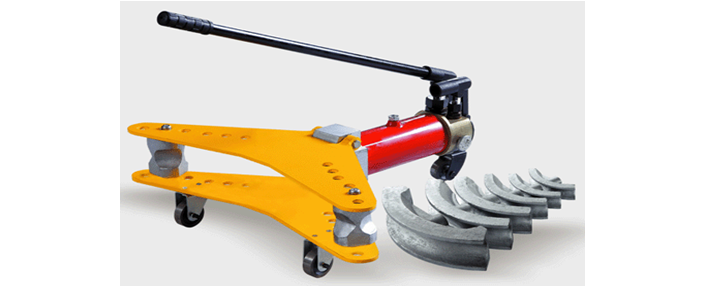
This type of buckling requires an adjustable bottom die. In three-point bending, the bottom die is not stationary and can be adjusted to any height within 0.01 mm. The upper tool and ram are both adjustable. The bending angle is controlled by the depth of the upper die into the V-groove of the lower die. Because this process requires less tools, it is generally more expensive than other forms of bending. However, it is used in highly-tech niche markets and is widely available.
Sheet Metal Bending Machine for Special Bending Dies
Special bending dies are required for the bending of parts of different shapes and sizes. These dies can be used in conjunction with a general bending die or separately. Generally, the bending dies are made with a curved or straight arm. The angle of the upper mold with smaller rounded corners is about 15 degrees and fillet radius is made in several fixed sizes. These are used for bending parts of varying thicknesses.
Depending on the metal, the bending force required varies. Keeping in mind that the bending force is highly dependent on the type of material, a good idea is to get a die with a lower yield strength. A die with a smaller opening can bend a material more efficiently, reducing the bending force. Once the desired angle is known, it will be easier to decide how much space the machine needs.
Press Brake for Sheet Metal Bending
A press brake for sheet metal bending machine uses a flat surface and a clamping bar to hold the material while the metal bends. The clamping action may be automatic or manual, and may be controlled by a foot pedal. A front gate-like plate is hinged and moves up and down to hold the material. As the material extends over the plate, the material will bend to follow its path.
The type of metal that will be bent will affect which press brake to use. High carbon steels are less bendable than aluminum alloys. This is due to their differences in strength and ductility. Also, each metal has a minimum bend radius that is recommended. To determine the ideal bending machine, the application and size of the material will determine which model and tonnage to purchase. For example, if a user intends to bend large sheets of metal, a higher tonnage will be better suited.
- Maintenance Tips for Vertical CNC Milling Machine in Iran’s Harsh Industrial Environment
- Market Potential for CNC Lathe Machines in South African Countries: Trends & Insights
- How Saudi Arabia’s Manufacturing Industry Rely on All Geared Radial Drilling Machines?
- Why All Geared Lathe Machines are Gaining Popularity in German Industry?
- Top Applications of Horizontal Boring Machines in Australian Manufacturing Industry
- The Growing Demand for All Geared Lathe Machines in Global Markets