Tips for Using a Press Brake
A Press Brake is a mechanical tool that is used for bending sheet or plate materials into predetermined shapes. It clamps the workpiece between a punch and die that match one another. A press brake is the most common type of bender. The following are tips and guidelines for using a Press Brake. Learn how to make the most of your machine by reading this article! Enjoy! This article has more tips on safety and maintenance!
Press Brake Techniques
There are several techniques used in the press brake operation. For example, you should know where the ram should be in relation to the stroke. Otherwise, you can injure or lose your fingers. This article will explain some of the techniques used in pressing brake operation. It also describes how to make your press brake work as efficiently as possible. This article will focus on two of the most common methods used in press brake operations. The first method is the best, and is often used for higher-volume press brakes.
Pressing brakes use tonnage and force to bend the metal. Tonnage is the total amount of pressure applied during the bending process. The higher the tonnage, the thicker the metal can be. The bending length determines the length of the sheet metal that can be bent. This calculation requires the use of a computer, and is an example of patent technology. It is important to choose the correct tonnage and length when using a press brake.
Press Brake Tooling
Press brake tooling is an integral part of the forming process. Its role is similar to that of the tires of a race car. They are the only part of the car that touches the ground, but are responsible for power, acceleration, and steering. Without proper tooling, the rest of the car hardware is useless and unmanageable. Here are some tips for using press brake tooling. First, choose the right type of tooling for the application.
First, inspect all press brake tools visually. Look for damaged surfaces, cracks, or bent sections. These defects could be the result of improper use and performance. If you see damaged tooling, toss it out immediately. Twenty-five years ago, it was rare to see damaged tools. In fact, mismatched punch and dies were much more common. As a result, suppliers have added a small stamping to their press brake tooling to identify the correct tooling for a specific application. Another way to identify the correct tooling for a specific application is by checking for a V-opening on a part’s surface. If the stamping isn’t visible, it may be due to a compromised tool material. This can lead to bad bending angles in the finished product.
Press Brake Safety
A well-designed press brake guarding system can prevent injuries to operators and maintain the machine’s productivity. The Sentinel is a mid-level press brake guarding system with laser transmitters and receivers. Its laser-guided safety shield protects the zone directly beneath the punch tip and enables the operator to hold a work piece. Its adjustable guarding is adjustable for operator comfort, efficiency, and general acceptance.
The press brake is a powerful and often deadly piece of machinery. Sadly, press brakes are among the most common causes of workplace amputations. These machines are often found in engineering workshops. While the guidance may not reflect current work health and safety regulations, it still contains useful information. Be sure to read this guidance alongside relevant industry standards. This guidance will be reviewed over time. To learn more about press brake safety, read on!
Press Brake Maintenance
For the effective functioning of your press brake, you should perform regular maintenance. You should replace the hydraulic oil regularly, and check the electrical cabinet. The back gauge should be in good condition. Make sure that it is set to the correct distance. You can also adjust the press brake to a predetermined distance, such as 100 mm. The back gauge can also be checked visually. Also, the bolts holding the wiper seal should be tested.
Regularly clean the hydraulic oil. It should be replaced when it becomes dirty or if it is clogged with dirt. Replace the oil filter if necessary. Make sure that the oil level is not too low or too high. If the hydraulic oil is too hot or too cold, install an oil heater or coolant. The hydraulic pump motor should be cleaned to remove dust and debris. It should be inspected regularly to ensure that it is performing correctly.
Buying a Press Brake
When buying a press brake, there are several things you should look for. First of all, determine the largest job you will need to do with the machine. If the job is large, you should choose a larger press brake than you actually need. When choosing a press brake, go up one size, and be sure to buy one with an extra foot of length. You never know when you’ll need to bend longer parts.
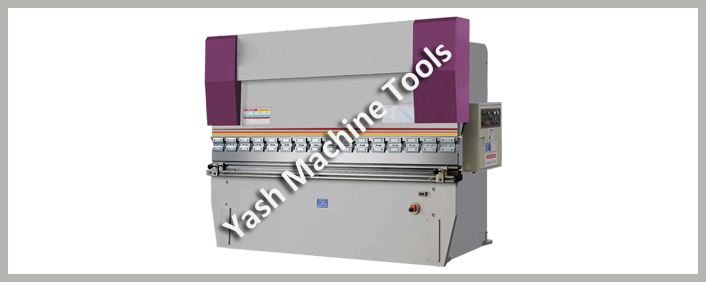
Second, make sure to consider the amount of parts you will be producing. If you’re only going to be using your press brake for a single job, you may want to go for a cheaper model with more features, or for multiple uses. In both cases, you need to make sure the machine is in good condition and has the best price/quality ratio. Another consideration is the material texture. Make sure to check out the deflection limit, as well as the price.
- Maintenance Tips for Vertical CNC Milling Machine in Iran’s Harsh Industrial Environment
- Market Potential for CNC Lathe Machines in South African Countries: Trends & Insights
- How Saudi Arabia’s Manufacturing Industry Rely on All Geared Radial Drilling Machines?
- Why All Geared Lathe Machines are Gaining Popularity in German Industry?
- Top Applications of Horizontal Boring Machines in Australian Manufacturing Industry
- The Growing Demand for All Geared Lathe Machines in Global Markets