How a Sheet Metal Bending Machine Works
A sheet metal bending machine is a cornerstone of modern metalworking, enabling industries to transform flat metal sheets into intricate shapes and structures with precision. From automotive components to enclosures for electrical equipment, these machines are pivotal in creating essential products we encounter daily. Understanding how a sheet metal bending machine works sheds light on its versatility, efficiency, and importance in manufacturing.
This article delves into the mechanics, capabilities, and design considerations associated with sheet metal bending machines, offering a comprehensive look at their functionality and role in modern industry.
What is a Sheet Metal Bending Machine?
A sheet metal bending machine is a specialized tool designed to bend and shape flat sheets of metal into desired forms. Using tools like punches and dies, it applies pressure to the sheet metal, forcing it into specific angles or curves. These machines are extensively used in industries such as automotive, aerospace, construction, and electronics.
The bending process is vital for producing components like brackets, panels, and enclosures, which are integral to various applications.
Core Components of a Sheet Metal Bending Machine
The functionality of a sheet metal bending machine relies on its core components, each contributing to precision and efficiency:
Punch and Die
- Punch: The upper tool that presses the metal into the desired shape.
- Die: The lower tool that supports the metal and helps form the bend.
Press Brake
- Provides the force required for bending by moving the punch or die.
- Available in hydraulic, mechanical, and servo-electric variants.
Back Gauge
- Ensures accurate positioning of the sheet metal for consistent bends.
- Essential for repeatability in mass production.
Control System
- Modern machines feature CNC (Computer Numerical Control) systems for precise programming of bend angles, lengths, and sequences.
How Does a Sheet Metal Bending Machine Work?
The operation of a sheet metal bending machine involves a series of steps designed to transform flat sheets into the desired shape with high precision.
Material Preparation
- The sheet metal is cleaned, cut to size, and positioned on the machine.
- The operator ensures the sheet is aligned correctly using the back gauge.
Tool Setup
- The punch and die are selected based on the material thickness and the required bend angle.
- These tools are installed and calibrated on the machine.
Bending Process
- The press brake applies force, moving the punch towards the die.
- The sheet metal is bent as it is forced between the punch and die.
- The depth of penetration determines the bend angle, while the back gauge ensures accuracy in positioning.
Quality Check
- After bending, the part is inspected for dimensional accuracy and surface quality.
- Adjustments are made to the machine settings if necessary.
Sheet Metal Bending Machine Capabilities
The sheet metal bending machine offers unparalleled versatility, capable of handling various materials, shapes, and production scales. Here are some key capabilities:
Precision Bending
- Achieves tight tolerances for critical applications.
- Ideal for producing parts like brackets, enclosures, and frames.
Multi-Axis Operations
- Advanced machines feature multi-axis control, enabling complex bends and intricate designs.
Material Flexibility
- Handles a wide range of metals, including aluminum, steel, stainless steel, and copper.
- Works with different thicknesses, from thin sheets to heavy-duty plates.
Mass Production
- CNC systems enable efficient batch production with consistent quality.
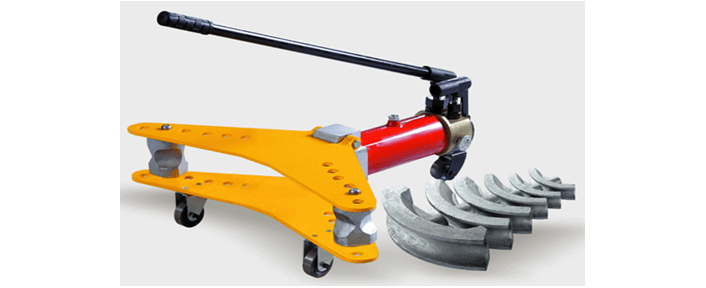
Types of Sheet Metal Bending Machines
Several types of sheet metal bending machines are available, each suited to specific tasks and industries:
Hydraulic Press Brake
- Uses hydraulic rams to generate bending force.
- Known for its power and ability to handle thick materials.
Servo-Electric Press Brake
- Powered by electric servo motors, offering precision and energy efficiency.
- Suitable for thin materials and intricate designs.
CNC Press Brake
- Features advanced CNC systems for automated operation.
- Ideal for complex and high-volume production.
Manual Bending Machines
- Operated manually, suitable for small-scale operations or simple bends.
Sheet Metal Part Design and Complexity
The sheet metal bending machine enables manufacturers to create parts of varying complexity, but design considerations play a crucial role in ensuring the success of the bending process.
Bend Radius
- The radius of the bend is influenced by the material properties and the punch-die configuration.
- A proper radius prevents cracking or deformation.
Material Springback
- Metal tends to spring back slightly after bending. This must be accounted for when setting the bend angle.
Multiple Bends
- The machine can perform multiple bends on a single piece, creating complex shapes like enclosures or brackets.
Part Consistency
CNC systems ensure repeatability and consistency in part dimensions, critical for industries like automotive and aerospace.
Advantages of Using a Sheet Metal Bending Machine
The sheet metal bending machine offers numerous benefits, making it an indispensable tool in metalworking industries:
High Precision
- Ensures accurate bends with minimal errors, even for intricate designs.
Increased Productivity
- Automated systems and efficient operations significantly reduce production time.
Versatility
- Capable of handling a variety of materials and shapes, catering to diverse industries.
Cost Efficiency
Reduces material wastage and labor costs through precision and automation.
Challenges in Sheet Metal Bending
Despite its advantages, operating a sheet metal bending machine comes with certain challenges:
Material Properties
- Differences in material hardness and thickness can affect bending results.
Tool Wear
- Prolonged use can lead to tool wear, impacting accuracy and surface quality.
Operator Expertise
- Skilled operators are essential for setting up the machine and troubleshooting issues.
By addressing these challenges with regular maintenance, quality tooling, and proper training, manufacturers can maximize the performance of their sheet metal bending machines.
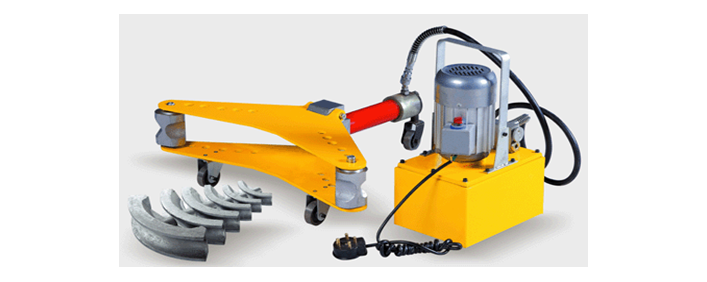
Future Trends in Sheet Metal Bending Machines
The evolution of the sheet metal bending machine continues, with advancements aimed at increasing efficiency and flexibility:
Automation and Robotics
- Integration with robotic arms for automated material handling and bending.
Smart Technology
- IoT-enabled machines that provide real-time monitoring and predictive maintenance.
Sustainability
- Development of energy-efficient machines to reduce the environmental footprint.
As these trends gain traction, the sheet metal bending machine will remain at the forefront of innovation in metalworking.

Conclusion
The sheet metal bending machine is a vital tool that has transformed the metalworking landscape. By combining advanced mechanics, precision tools, and intelligent systems, these machines deliver exceptional results in creating intricate metal parts. Understanding how a sheet metal bending machine works reveals the complexity and ingenuity behind its operation, showcasing why it is an indispensable asset in industries worldwide.
From simple brackets to complex enclosures, the versatility and efficiency of the sheet metal bending machine continue to drive progress in manufacturing and innovation.
- Main Features of Vertical CNC Milling Machines
- Understanding the Working Principles of a CNC Lathe Machine
- Top Applications of Radial Drilling Machines in Manufacturing and Construction
- The Advantages of Radial Drilling Machines in Heavy-Duty Industries
- Precision Cutting Redefined: The Unmatched Benefits of Bandsaw Machines