Main Features of Vertical CNC Milling Machines
Vertical CNC milling machines are essential in modern manufacturing, known for their precision, versatility, and efficiency. These machines are used across industries such as aerospace, automotive, electronics, and general manufacturing to create intricate parts with high accuracy. What sets vertical CNC milling machines apart are their advanced features, which ensure outstanding performance and reliability.
This article explores the main features of vertical CNC milling machines, focusing on their high rigidity, precision, speed, and innovative systems that enhance productivity and quality.
High Rigidity and High Stability in CNC Milling Machine Structure
The structural integrity of a vertical CNC milling machine is crucial for achieving precision and reliability during machining operations. These machines are built with a rigid and stable structure designed to withstand high forces and vibrations without compromising accuracy.
Key Structural Features:
- Heavy-Duty Frame: The machine frame is typically made of cast iron or high-strength steel, providing excellent damping properties and resistance to deformation.
- Stable Base: A wide, stable base ensures that the machine remains anchored during high-speed operations, reducing the likelihood of vibrations.
- Column Design: The vertical column is reinforced to handle the cutting forces generated during machining, ensuring consistent tool performance.
Benefits:
- Improved machining accuracy, even during high-speed operations.
- Enhanced durability and longevity of the machine.
- Ability to handle large and heavy workpieces without losing stability.
The high rigidity and stability of vertical CNC milling machines make them ideal for producing components that require tight tolerances and impeccable surface finishes.
High Precision Three-Axis Feeding System
One of the standout features of a vertical CNC milling machine is its three-axis feeding system, which ensures precise movements along the X, Y, and Z axes. This system is pivotal for executing intricate machining tasks and maintaining dimensional accuracy.
Components of the Feeding System:
- Linear Guideways: These guideways reduce friction, enabling smooth and precise motion of the machine’s moving parts.
- Ball Screws: High-quality ball screws convert rotary motion into linear motion with minimal backlash, ensuring exact positioning of the cutting tool.
- Servo Motors: Advanced servo motors provide precise control over movement, enhancing the accuracy of the feed system.
Advantages:
- Accurate tool positioning for complex machining tasks.
- Consistent dimensional accuracy, even for large batch production.
- Reduced wear and tear due to low-friction components.
This high-precision feeding system is a cornerstone of vertical CNC milling machines, making them suitable for industries where accuracy is non-negotiable, such as aerospace and medical device manufacturing.
High-Speed Precision Spindle
The spindle is the heart of any milling machine, and in vertical CNC milling machines, high-speed precision spindles are engineered to deliver exceptional performance. These spindles ensure optimal cutting conditions, even at high rotational speeds.
Key Features of High-Speed Spindles:
- Variable Speed Control: Allows operators to adjust spindle speeds to match the material and cutting requirements.
- Direct Drive Motors: Provide high torque and eliminate the need for gears, reducing noise and wear.
- High-Precision Bearings: Support smooth spindle rotation, ensuring stability at high speeds.
Benefits of a High-Speed Spindle:
- Faster material removal rates, increasing productivity.
- Superior surface finishes due to consistent cutting speeds.
- Reduced cycle times for complex machining operations.
With a high-speed precision spindle, vertical CNC milling machines can handle various materials, from soft plastics to tough alloys, while maintaining quality and efficiency.
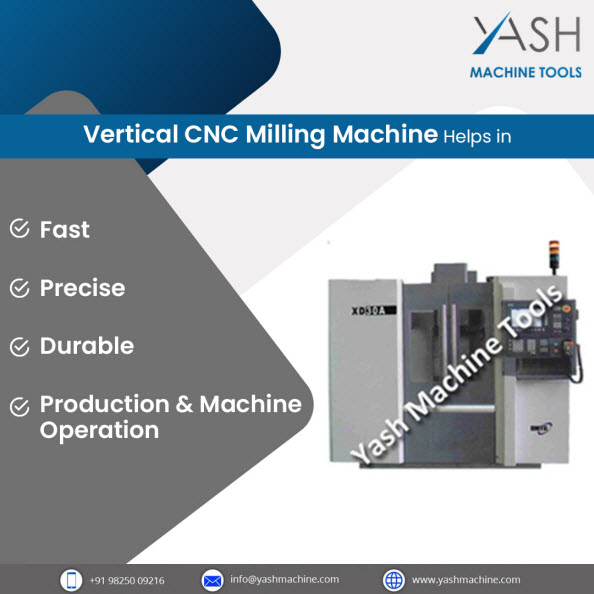
Fast and Reliable Tool Changing Mechanism
Efficiency in machining is not just about cutting speed; it also involves minimizing downtime during tool changes. Vertical CNC milling machines feature advanced tool changing mechanisms that ensure quick and accurate tool swaps.
Types of Tool Changers:
- Automatic Tool Changers (ATC): Use robotic arms or rotating carousels to quickly switch tools based on the programmed sequence.
- Dual-Arm Tool Changers: Reduce tool change time by simultaneously handling the used and next tool.
- Turret Systems: Provide an alternative for specific vertical milling machine configurations.
Advantages:
- Reduced idle time between operations, boosting overall productivity.
- Accurate tool alignment, ensuring continuity in machining processes.
- Ability to accommodate multiple tools for complex jobs without manual intervention.
The fast and reliable tool-changing mechanism in vertical CNC milling machines enhances operational efficiency, making them an invaluable asset for high-volume manufacturing.
Advanced Cooling System
Machining processes generate significant heat due to friction between the cutting tool and the workpiece. A robust cooling system is essential to prevent overheating, maintain tool integrity, and ensure consistent machining quality.
Key Cooling System Features:
- Flood Coolants: Deliver a steady stream of coolant to the cutting zone, reducing heat and flushing away chips.
- Mist Coolants: Use a fine mist of lubricant for materials requiring minimal cooling.
- Through-Spindle Coolant: Delivers coolant directly through the spindle to reach the cutting edge.
Benefits of a Cooling System:
- Prolonged tool life by minimizing thermal wear.
- Improved surface finish due to consistent cutting temperatures.
- Enhanced machining accuracy by reducing thermal expansion in the workpiece and machine components.
An advanced cooling system in vertical CNC milling machines is crucial for achieving reliable performance, particularly during high-speed or prolonged operations.
High-Performance Electric Control System
The electric control system is the brain of a vertical CNC milling machine, orchestrating all operations and ensuring seamless communication between components. This system allows for precise execution of programmed instructions, enhancing the machine’s functionality and user experience.
Features of the Electric Control System:
- CNC Control Unit: Executes G-code and manages tool paths, spindle speeds, and feed rates.
- User-Friendly Interface: Provides operators with intuitive controls for programming, monitoring, and troubleshooting.
- Sensors and Feedback Systems: Continuously monitor performance parameters like spindle speed, tool position, and temperature.
Advantages:
- Improved reliability and efficiency in executing complex machining tasks.
- Real-time monitoring and diagnostics to prevent errors and downtime.
- Enhanced safety features, including emergency stop mechanisms.
With a high-performance electric control system, vertical CNC milling machines can achieve unparalleled precision, adaptability, and ease of operation.

Conclusion
Vertical CNC milling machines have redefined manufacturing by combining high rigidity, precision, speed, and advanced systems. From their robust structural design to their efficient cooling and control mechanisms, every feature is engineered to enhance performance and reliability. These machines cater to diverse machining needs, offering consistent quality and productivity for industries requiring precision and efficiency.
By understanding the main features of vertical CNC milling machines, businesses can make informed decisions about integrating these advanced tools into their operations. Whether it’s producing intricate aerospace components, high-quality medical devices, or automotive parts, vertical CNC milling machines are the backbone of modern manufacturing.
- Maintenance Tips for Vertical CNC Milling Machine in Iran’s Harsh Industrial Environment
- Market Potential for CNC Lathe Machines in South African Countries: Trends & Insights
- How Saudi Arabia’s Manufacturing Industry Rely on All Geared Radial Drilling Machines?
- Why All Geared Lathe Machines are Gaining Popularity in German Industry?
- Top Applications of Horizontal Boring Machines in Australian Manufacturing Industry
- The Growing Demand for All Geared Lathe Machines in Global Markets