Understanding the Working Principles of a CNC Lathe Machine
CNC (Computer Numerical Control) lathe machines have revolutionized the manufacturing world by offering unparalleled precision, efficiency, and automation in machining operations. These advanced tools are essential in industries ranging from automotive and aerospace to electronics and medical device manufacturing. But what makes a CNC lathe machine tick? In this comprehensive guide, we’ll dive into the working principles of CNC lathe machines, exploring how they operate, their components, and the processes they perform.
What is a CNC Lathe Machine?
A CNC lathe machine is a computer-controlled tool designed to perform a variety of machining tasks, including turning, facing, threading, drilling, and more. Unlike traditional manual lathes, CNC lathes are automated and rely on programmed instructions (G-code) to execute precise operations. This eliminates human errors, ensures repeatability, and improves production efficiency.
Core Components of a CNC Lathe Machine
To understand the working principles, it’s crucial to know the key components of a CNC lathe machine and their functions:
Headstock
- Houses the main spindle, which holds and rotates the workpiece.
- Includes speed controls to regulate the spindle’s rotational velocity.
Chuck
- A gripping mechanism mounted on the spindle to securely hold the workpiece in place during machining.
Bed
- The base structure that supports the machine components, ensuring rigidity and stability.
Tailstock
- Used to support the workpiece on its opposite end, especially during operations requiring high precision, like long workpieces.
Tool Turret
- Holds multiple cutting tools and rotates to bring the required tool into position during machining.
CNC Control Panel
- The interface where operators input commands and monitor machine operations.
Guideways and Slides
- Allow the movement of the tool along the X-axis (radial) and Z-axis (longitudinal) to perform cutting operations.
Coolant System
- Delivers coolant to the cutting zone to reduce heat, minimize tool wear, and improve surface finish.
Working Principles of a CNC Lathe Machine
The operation of a CNC lathe machine revolves around the integration of mechanical components, computer systems, and precision programming. Here’s a step-by-step breakdown of how a CNC lathe machine works:
Loading the Workpiece
- The process begins with securely mounting the workpiece in the chuck. The chuck ensures that the workpiece is held firmly and rotates around the spindle axis.
Inputting the Program
- Operators use G-code, a standardized programming language, to input machining instructions into the CNC control panel. The program specifies:
- Tool paths
- Spindle speed
- Cutting feed rate
- Depth of cut
- Sequence of operations
Tool Selection and Positioning
- The tool turret rotates to bring the required cutting tool into position. These tools are pre-set with offsets to ensure precision in every operation.
Spindle Operation
- The spindle starts rotating, spinning the workpiece at the programmed speed. The speed varies depending on the material and the type of machining operation being performed.
Cutting Operations
- The cutting tool is moved along the workpiece according to the programmed tool path. Common operations include:
- Turning: Removing material from the outer diameter to achieve a cylindrical shape.
- Facing: Creating a flat surface by cutting perpendicular to the spindle axis.
- Threading: Forming threads along the workpiece.
- Grooving: Cutting a narrow channel in the workpiece.
- Drilling: Creating holes along the workpiece’s axis.
Coolant Application
- The coolant system continuously sprays liquid to the cutting zone, ensuring temperature control and maintaining cutting tool efficiency.
Continuous Monitoring
- Sensors and feedback systems continuously monitor tool positions, cutting forces, and spindle speeds, ensuring precise adherence to the programmed instructions.
Completion and Unloading
- Once the machining process is complete, the spindle stops, and the workpiece is removed from the chuck. The final product undergoes inspection to verify dimensional accuracy.
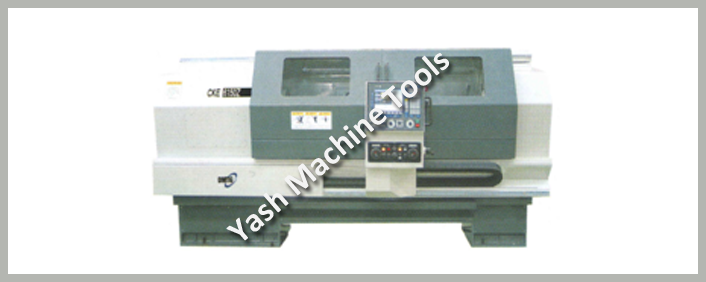
Key Advantages of CNC Lathe Machines
Understanding how CNC lathe machines work also highlights their numerous advantages:
Precision and Accuracy
- CNC lathe machines operate with extreme precision, achieving tolerances as tight as a few microns. This is critical for industries requiring high-quality components.
Repeatability
- Once a program is set, the machine can replicate the same product multiple times without deviation, ensuring consistency in mass production.
Versatility
- From simple turning tasks to intricate threading and grooving, CNC lathe machines can perform a wide range of operations.
Reduced Labor Costs
- Automation minimizes the need for manual intervention, reducing labor costs and increasing production efficiency.
Safety
- Operators are removed from the direct machining process, reducing the risk of injuries from moving parts and sharp tools.
Applications of CNC Lathe Machines
The working principles of CNC lathe machines enable their use across various industries, including:
Automotive Industry
- Producing engine parts like crankshafts and pistons.
- Manufacturing threaded components such as bolts and screws.
Aerospace Industry
- Creating precision components for aircraft engines and landing gears.
Electronics Industry
- Producing tiny components like connectors and housings.
Medical Industry
- Crafting surgical instruments and prosthetics with high accuracy.
General Manufacturing
- Producing custom tools, molds, and machine parts.
CNC Lathe Machine Tools and Their Functions
The versatility of a CNC lathe machine stems from the variety of tools it uses. Each tool is designed for a specific function:
Turning Tool
- Removes material from the outer diameter of the workpiece.
Boring Tool
- Enlarges existing holes to precise diameters.
Threading Tool
- Creates external or internal threads along the workpiece.
Grooving Tool
- Cuts narrow channels into the workpiece surface.
Drilling Tool
- Drills holes along the axis of the workpiece.
Parting Tool
- Separates a finished part from the rest of the workpiece.
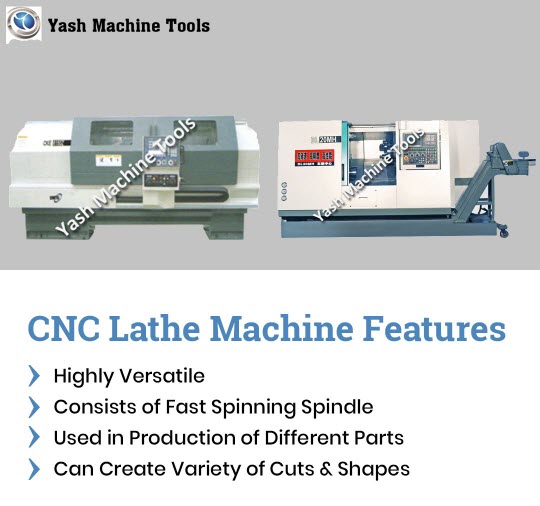
Maintenance of CNC Lathe Machines
To ensure the smooth operation of a CNC lathe machine, regular maintenance is essential:
Daily Maintenance
- Clean the machine to remove chips and debris.
- Check the coolant level and refill if necessary.
- Inspect tools for wear and replace as needed.
Weekly Maintenance
- Lubricate moving parts such as slides and guideways.
- Inspect the chuck and spindle for alignment.
Monthly Maintenance
- Perform a thorough inspection of electrical systems and sensors.
- Test the accuracy of tool offsets and recalibrate if necessary.
The Future of CNC Lathe Machines
With advancements in technology, CNC lathe machines are becoming even more sophisticated. Features like IoT integration, real-time monitoring, and AI-driven predictive maintenance are making these machines smarter and more efficient. As industries continue to demand higher precision and automation, CNC lathe machines will remain at the forefront of modern manufacturing.

Conclusion
The working principles of a CNC lathe machine showcase the seamless integration of mechanical engineering and computer technology. By automating complex machining operations with precision, these machines have transformed industries and set new benchmarks for productivity and quality. Whether you’re a manufacturer producing intricate aerospace components or a workshop crafting custom tools, the CNC lathe machine is an indispensable asset that combines innovation with efficiency.
- Maintenance Tips for Vertical CNC Milling Machine in Iran’s Harsh Industrial Environment
- Market Potential for CNC Lathe Machines in South African Countries: Trends & Insights
- How Saudi Arabia’s Manufacturing Industry Rely on All Geared Radial Drilling Machines?
- Why All Geared Lathe Machines are Gaining Popularity in German Industry?
- Top Applications of Horizontal Boring Machines in Australian Manufacturing Industry
- The Growing Demand for All Geared Lathe Machines in Global Markets